Porosity in Welding: Identifying Common Issues and Implementing Best Practices for Avoidance
Porosity in welding is a pervasive issue that usually goes undetected until it creates considerable troubles with the stability of welds. In this conversation, we will check out the key aspects adding to porosity development, examine its destructive impacts on weld performance, and go over the best techniques that can be embraced to decrease porosity occurrence in welding processes.
Usual Reasons For Porosity
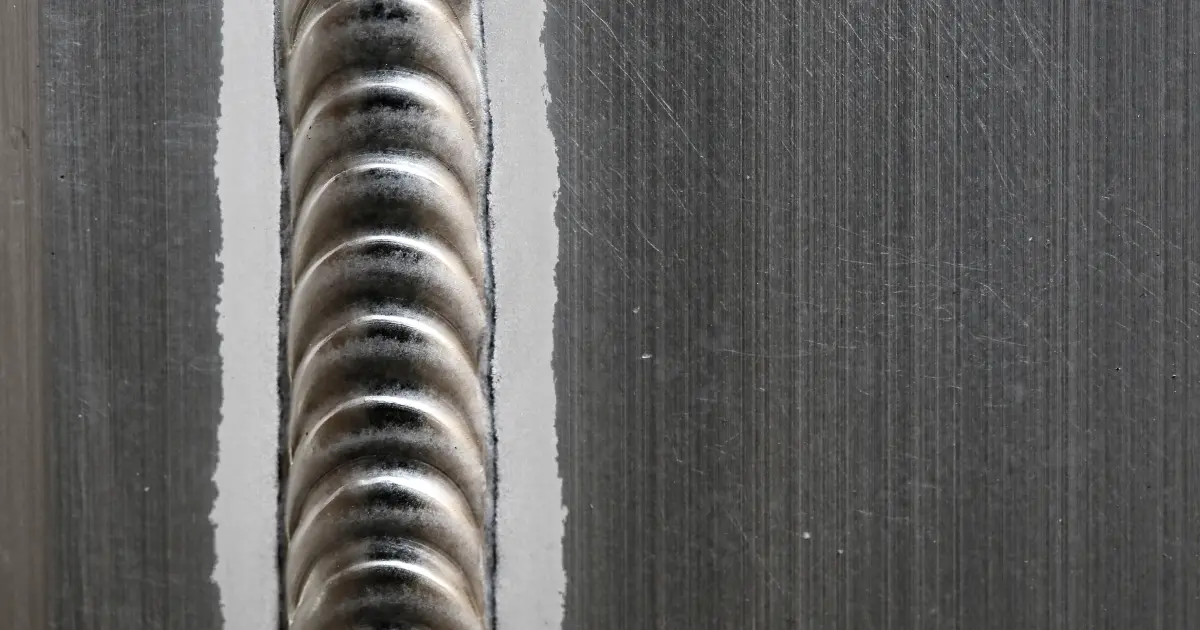
An additional regular offender behind porosity is the visibility of impurities externally of the base metal, such as oil, grease, or rust. When these contaminants are not efficiently eliminated before welding, they can evaporate and become caught in the weld, causing flaws. In addition, making use of unclean or damp filler products can introduce impurities into the weld, contributing to porosity issues. To reduce these typical root causes of porosity, complete cleaning of base metals, correct shielding gas option, and adherence to optimal welding parameters are crucial techniques in achieving high-quality, porosity-free welds.
Effect of Porosity on Weld Quality

The visibility of porosity in welding can dramatically jeopardize the structural stability and mechanical residential properties of welded joints. Porosity creates gaps within the weld metal, damaging its general stamina and load-bearing capacity. These spaces act as tension focus factors, making the weld much more susceptible to splitting and failure under applied lots. Furthermore, porosity can reduce the weld's resistance to rust and various other environmental aspects, further decreasing its long life and performance.
One of the main repercussions of porosity is a decline in the weld's ductility and toughness. Welds with high porosity levels have a tendency to display reduced impact toughness and decreased capacity to warp plastically prior to fracturing. This can be particularly concerning in applications where the welded components are subjected to dynamic or cyclic loading problems. Furthermore, porosity can hinder the weld's ability to effectively transmit forces, resulting in premature weld failure and prospective security dangers in essential frameworks.
Finest Practices for Porosity Avoidance
To improve the architectural honesty and quality of welded joints, what specific measures can be applied to decrease the event of porosity throughout the welding process? Using the appropriate welding method for the certain product being bonded, such as readjusting the welding angle and gun placement, can even more prevent porosity. Normal examination of welds and instant removal of any type of problems determined throughout the welding process are necessary techniques to protect against porosity and produce top notch welds.
Importance of Proper Welding Strategies
Carrying out correct welding strategies is vital in guaranteeing the structural integrity and quality of welded joints, building on the structure of reliable porosity prevention measures. Welding methods look at these guys straight impact the total toughness and toughness of the bonded structure. One essential aspect of correct welding techniques is maintaining the proper warmth input. Extreme warmth can lead to boosted porosity due to the entrapment of gases in the weld swimming pool. Alternatively, insufficient heat may cause incomplete blend, producing prospective powerlessness in the joint. Furthermore, utilizing the appropriate welding specifications, such as voltage, existing, and travel speed, is crucial for accomplishing sound welds with very little porosity.
Furthermore, the option of welding process, whether it be MIG, TIG, or click here to find out more stick welding, ought to straighten with the details needs of the task to guarantee optimal outcomes. Appropriate cleaning and prep work of the base steel, as well as selecting the best filler product, are also crucial components of competent welding techniques. By sticking to these ideal techniques, welders can minimize the risk of porosity formation and produce top quality, structurally sound welds.
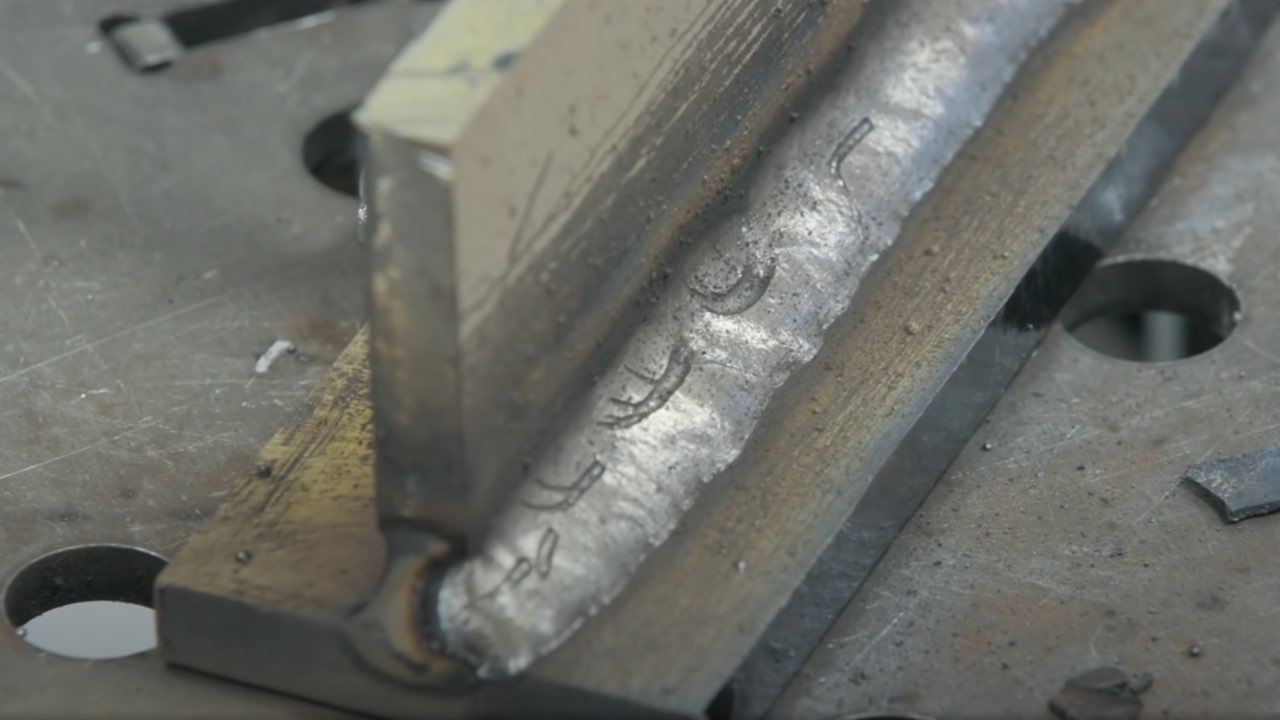
Evaluating and Quality Assurance Measures
Testing procedures are vital to find and stop porosity in welding, ensuring the strength and resilience of the final product. Non-destructive screening approaches such as ultrasonic screening, radiographic screening, and visual inspection are generally employed to determine potential issues like porosity.
Post-weld assessments, on the various other hand, analyze Get the facts the last weld for any type of defects, including porosity, and validate that it satisfies specified standards. Applying a thorough top quality control strategy that includes detailed screening procedures and inspections is vital to lowering porosity issues and guaranteeing the general quality of bonded joints.
Final Thought
To conclude, porosity in welding can be an usual problem that influences the quality of welds. By recognizing the typical root causes of porosity and implementing ideal methods for prevention, such as correct welding strategies and screening measures, welders can ensure top quality and reputable welds. It is essential to focus on prevention techniques to minimize the incident of porosity and maintain the stability of bonded structures.
Comments on “Professional Suggestions on What is Porosity in Welding and How to Resolve It”